Molding Precision: The Cornerstone of Metal Fabrication
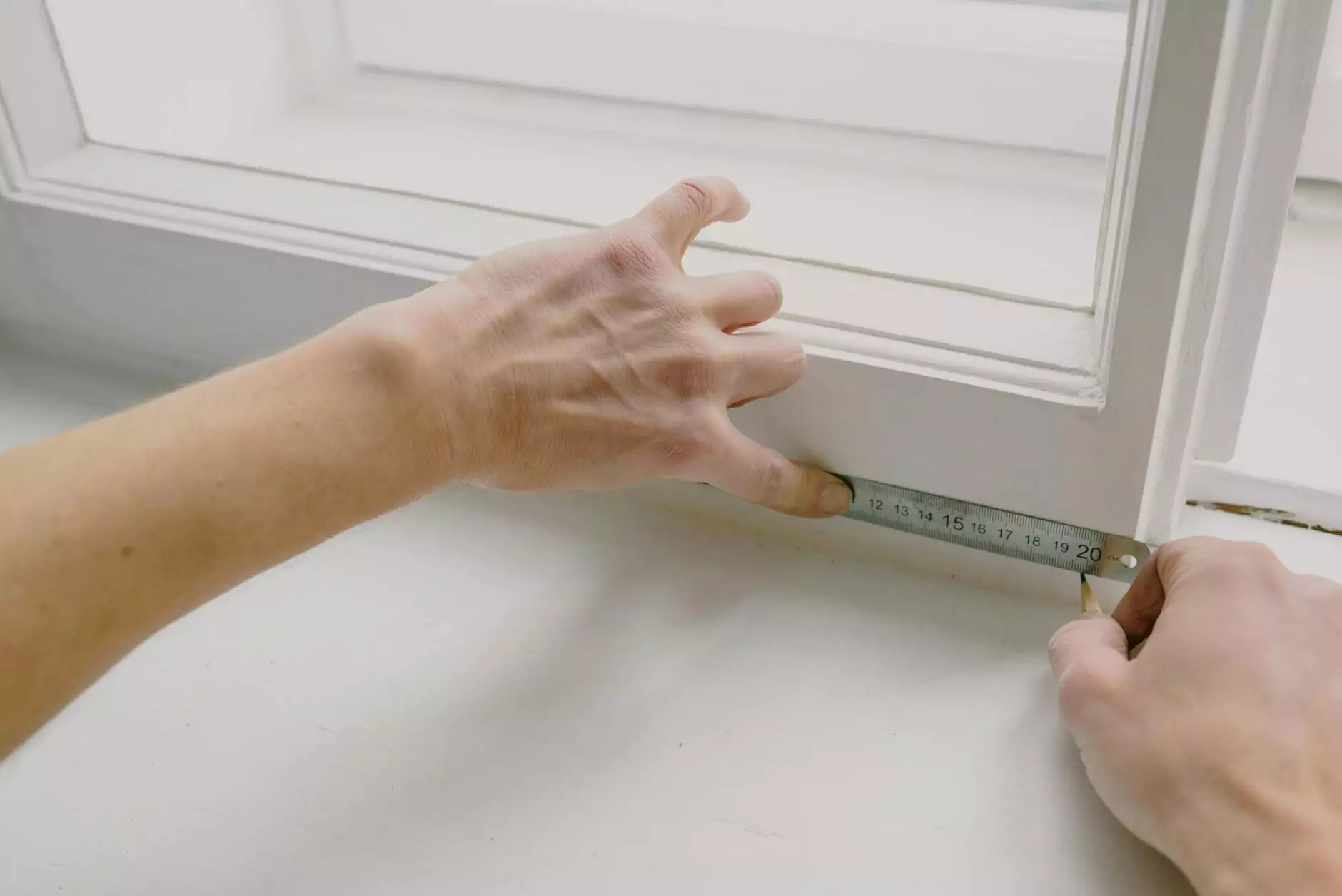
In the highly competitive landscape of metal fabrication, businesses constantly seek methods to enhance efficiency and achieve unparalleled quality. One such pivotal aspect is molding precision, a term that embodies the meticulous craft required to produce components that meet exact specifications. In this comprehensive article, we will delve into the significance of molding precision, its integral role in metal fabrication, and how businesses like DeepMould.net are leveraging this principle to gain a competitive edge.
Understanding Molding Precision
At its core, molding precision refers to the accuracy and exactness in the manufacturing process where metal is shaped into specific forms or components. Achieving molding precision involves careful control of various factors, including:
- Material Selection: Choosing the right type of metal is crucial for achieving desired properties.
- Design Specifications: Precise engineering drawings ensure that components are built to exact dimensions.
- Advanced Machinery: Utilizing state-of-the-art equipment enhances the precision of the molding process.
- Skilled Labor: Highly-trained professionals can execute complex tasks that demand meticulous attention to detail.
The Importance of Molding Precision in Metal Fabrication
The significance of molding precision extends beyond mere aesthetics; it fundamentally influences product quality, production efficiency, and overall business success. Here are several reasons why molding precision is crucial in the realm of metal fabrication:
1. Enhanced Product Quality
Products that are fabricated with molding precision exhibit higher quality standards. When components are shaped correctly, they fit perfectly during assembly, which leads to:
- Reduced Defects: With precise molding, the incidence of defects is minimized, leading to fewer reworks.
- Improved Functionality: Components that fit well perform their intended functions efficiently.
- Longer Lifespan: Accurate parts are less likely to wear or break, increasing their lifespan.
2. Cost Efficiency
Investing in molding precision can lead to significant long-term cost savings. Here’s how:
- Fewer Material Wastes: Precision reduces the amount of material wasted during production.
- Less Assembly Time: Well-molded components require less time to assemble, which translates to lower labor costs.
- Reduced Maintenance Costs: High-quality parts reduce downtime and maintenance expenses in the long run.
3. Stronger Market Position
Companies renowned for their commitment to molding precision gain a stellar reputation within the industry. As a result, they can:
- Attract More Clients: High standards of precision often translate to higher customer satisfaction.
- Diverse Product Offerings: With the ability to produce precise components, companies can expand their product lines.
- Establish Long-term Partnerships: Businesses that provide precise and reliable products often foster strong relationships with clients and suppliers.
Strategies for Achieving Molding Precision
For businesses in the metal fabrication industry, achieving molding precision is paramount. Here are effective strategies that can be implemented:
1. Invest in Advanced Machinery
The choice of machinery can have a considerable impact on the molding process. Investing in modern equipment equipped with:
- Computer Numerical Control (CNC): CNC machines can produce complex shapes with high precision.
- Laser Cutting Technology: This technology enhances the accuracy of cuts, ensuring perfect dimensions.
- Robotics: Automation improves consistency in the manufacturing process.
2. Implement Quality Control Measures
Quality assurance is essential after the molding process. Implementing stringent quality control measures such as:
- Regular Inspections: Frequent checks on finished products for dimensional accuracy.
- Testing Procedures: Conducting functionality tests to ensure parts meet specifications.
- Feedback Loops: Establishing systems to gather feedback and make necessary adjustments in processes.
3. Continuous Employee Training
The workforce is the backbone of any manufacturing operation. Continually training employees on:
- Latest Manufacturing Techniques: Exposure to new methodologies enhances skill sets.
- Equipment Use: Ensuring that staff members are proficient in operating advanced machinery.
- Safety Protocols: Keeping the workspace safe and minimizing risks to improve productivity.
Case Studies: Successful Implementation of Molding Precision
Multiple companies in the metal fabrication industry have exemplified excellence through molding precision. Below are a few case studies showcasing their achievements:
Case Study 1: DeepMould.net
DeepMould.net is a prominent metal fabricator known for its dedication to molding precision. By adopting cutting-edge CNC machinery and implementing rigorous quality control standards, they have:
- Increased Production Efficiency: Achieving a 30% reduction in production time while ensuring high-quality outputs.
- Expanded Client Base: Delivering precision-engineered components led to partnerships with major industry players.
- Enhanced Customer Satisfaction: High-quality products have resulted in a significant increase in repeat business.
Case Study 2: Precision Metal Works
Another example is Precision Metal Works, which focused on molding precision by investing in laser cutting technology. Their efforts led to:
- Improved Material Utilization: Optimizing the cutting process to reduce waste.
- Faster Turnaround Times: By streamlining production processes, they significantly improved delivery times.
- Stronger Customer Loyalty: Providing consistently high-quality products cultivated strong relationships and repeat orders.
Conclusion: The Future of Molding Precision in Metal Fabrication
As we venture further into the future, the role of molding precision in metal fabrication will only grow in significance. Companies that prioritize precision will be better positioned to:
- Meet Evolving Industry Standards: As technologies evolve, so do customer expectations; precision will be a key factor.
- Adapt to New Markets: Precision can open doors to industries that demand high-quality components, such as aerospace and automotive.
- Drive Innovation: Companies that uphold high standards of precision are often at the forefront of innovation.
Ultimately, businesses like DeepMould.net are setting the standard for what it means to achieve molding precision. Their commitment to quality not only strengthens their market position but also elevates the entire industry, making it imperative for others to follow suit. As molding precision remains a critical component of successful metal fabrication, the pursuit of accuracy, quality, and innovation will dictate the future landscape of this dynamic industry.